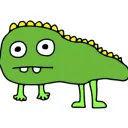
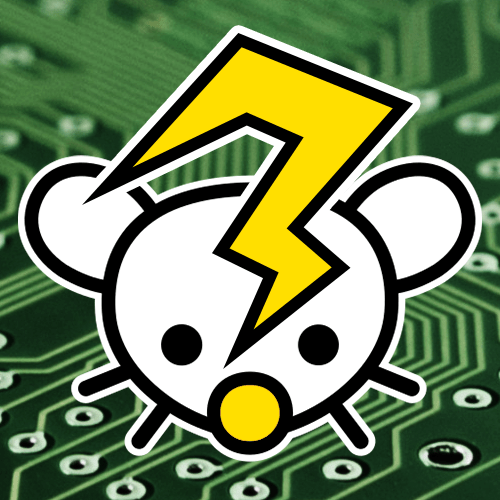
You will probably need to increase your voltage. I haven’t ever used the LM334, but it will need a minimum voltage across it. I don’t know if you are still using the IRFP250N, but if so it has a threshold somewhere between 2V and 4V for 250uA, so the threshold won’t be as high but it should be close. I would try using 5V if it’s fine with your setup.
For the suitability of the resistor method, you should do the math on how a change in Vds will affect the current, and then calculate how much this variability in current will affect your readings. If this error/innacuracy is acceptable, then why not.
You will need to provide a voltage of at least the threshold voltage PLUS the minimum voltage of the LM334Z. If the LM334Z circuit by itself doesn’t work, that will be the first problem to figure out. Make sure you completely read through the datasheet https://www.ti.com/lit/ds/symlink/lm334.pdf?ts=1689139734046&ref_url=https%253A%252F%252Fwww.google.com%252F, there are example circuits in it for reference. For the resistor method, keep in mind that the current isn’t constant; the voltage is. Your current is dictated by your resistor and the voltage across it, which is the supply voltage minus the threshold voltage. If your threshold voltage changes as the dose increases (which is the typical behaviour), the voltage across the resistor will change, therefore your current will change, which will generate error in your reading. The only way to minimize this error is to apply a very high voltage (100’s to 1000’s of volts) to the resistor, such that a change in the threshold would become a rounding error.